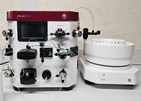
While the AKTA Start is significantly less maintenance intensive compared to some of the other system models within the AKTA range, there are still some best practices to carry out to ensure you are optimizing your systems performance.
In addition to the Original Equipment Manufacturer (OEM) guidelines, we have created a checklist to help with routine inspections:
Daily (before use)
-
As with any Chromatography System it is always best to visually inspect for signs of leaks and check for kinks in the peek tubing. Inspect around and below the pump module and connection points along the flow path.
-
Inspect the pump tubing for signs of excessive wear and verify that it is securely connected on both sides of the pump head. Proper installation is crucial, straighten the tubing to ensure a snug fit against the rotor inside the pump head. Use the provided clamps to secure the tubing, preventing loosening or displacement during operation.
When the system is not in use, open the pump head to release pressure on the tubing. Leaving the pump head closed can lead to unnecessary wear and significantly reduce the tubing's lifespan.
-
Perform the System cleaning methods before and after use with DI water before and with 1 M NaOH after use.
-
Clean the sample valve after use with either DI water or 1 M NaOH. The A and B valves are cleaned during the System wash method. To clean the Sample valve, select Execute Manual Instructions and set the sample valve to Sample, wash valve to Column and the outlet to Waste. Set the flow to 5ml/min and perform a manual run for 5 minutes.
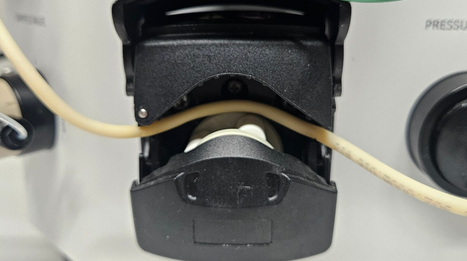
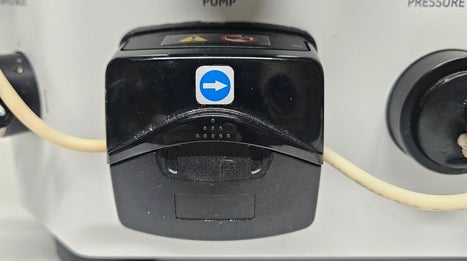
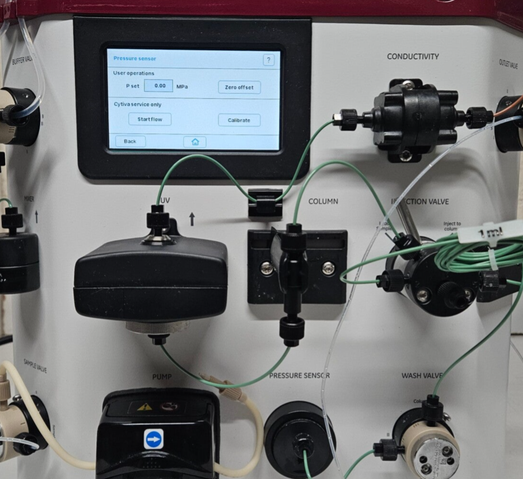
Weekly
-
Inspect and clean the inlet filters. Submerge net and filters in 1 M NaOH for up to 2 hours and rinse with DI water. Use an ultrasonic bath if you have one available.
- Perform pump calibration using a pre-weighed tube, following the instructions outlined on page 78 of the AKTA Start maintenance manual. For optimal accuracy, set the flow rate to approximately 2.5 ml/min and conduct the test for at least one to two minutes.
- Check the tubing connections for salt deposits, as excessive build-up may indicate a leak. If ignored, this could cause a snapped connector during future disassembly.
- Verify the pressure monitor. Disconnect the tubing connected to the monitor and confirm the zero-pressure reading is within ±0.02MPa. Perform calibration If the reading is outside this range which can be performed via the instrument display panel and selecting Settings and Service, Pressure Sensor.
- Clean the exterior of the instrument and fraction collector, paying attention to the tubing connection points and pumps.
Monthly
-
Clean the pump head to prevent the build-up of residue and contaminants. Ensure the instrument is switched off to prevent accidental operation of the pump rollers. Wipe down the rollers, clamps and covers.
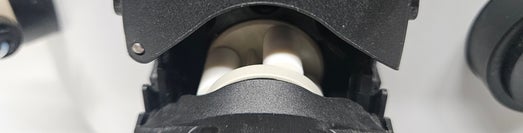
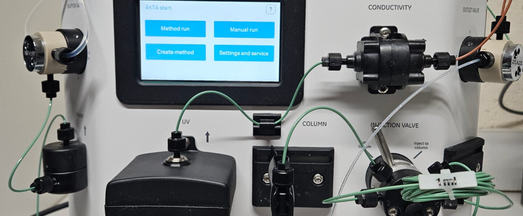
6 Monthly
- Clean the UV flow cell. Using 10% detergent solution fill the flow cell and Leave for 15 minutes. Flush the cell thoroughly with DI water.
- Clean the Conductivity flow cell. Fill the flow cell with 1 M NaOH for 15 minutes and flush with DI water.
- Consider performing a system test every six months to verify the pump, monitors and fraction collector are functioning within specification.
12 Monthly
Annual Preventive Maintenance (PM) is recommended and should include the following tasks:
- Inspect the drive sleeve and conduct the feed tube and home tests. Ensure the feed tube test stops correctly at all positions. If either test fails or the drive sleeve appears worn, replace the sleeve to maintain optimal performance.
- Pump tubing replacement (If required)
- Inlet filter replacement
- UV & Conductivity verification (including UV diagnostic tests)
- System performance test
Additional inspections and tests may be necessary for your Preventive Maintenance (PM) schedule or may need to be performed more frequently if required. To determine the appropriate maintenance level and frequency for your instrument, consider the following factors:
- Instrument Use - Is your instrument used regularly? Are there prolonged periods of down time?
- Process Criticality - What is the impact to your process and cost implication if your instrument fails during operation?
- Compliance - Is your instrument compliant and maintained accordingly?
At Service Lab, we offer customised maintenance solutions for your AKTA Start instrument. Feel free to contact us to discuss your specific requirements.
The provided publication 'ÄKTA Start Maintenance Manual' is for information purposes only. © Copyright Cytiva – Reproduced by permission of the owner.
Add comment
Comments